Inhaltsverzeichnis:
Einleitung: Was ist Produktion 3.0 und Produktion 4.0?
Die industrielle Fertigung hat im Laufe der Zeit eine beeindruckende Entwicklung durchlebt. Die Begriffe Produktion 3.0 und Produktion 4.0 stehen für zwei wesentliche Phasen dieser Evolution. Produktion 3.0 bezeichnet einen Produktionsprozess, der vor allem durch die Automatisierung charakterisiert ist, bei dem Roboter und automatische Fertigungslinien die Effizienz steigern. Diese Phase ist geprägt von der weiteren Digitalisierung und Vernetzung innerhalb einzelner Maschinen und Anlagen.
Im Gegensatz dazu steht Produktion 4.0, welche auch als vierte industrielle Revolution oder Industrie 4.0 bezeichnet wird. Diese Ära nutzt die fortschreitende Digitalisierung, um eine noch weitergehende Vernetzung aller an der Produktion beteiligten Elemente zu ermöglichen. Hier spielen Technologien wie das Internet der Dinge (IoT), Big Data und künstliche Intelligenz (KI) eine zentrale Rolle. Sie ermöglichen eine intelligentere und flexiblere Produktion, in der Systeme selbstständig Entscheidungen treffen und sich in Echtzeit an Veränderungen anpassen können.
Während Produktion 3.0 vorrangig die Effizienz durch Automatisierung verbesserte, treibt Produktion 4.0 die Optimierung weiter voran, indem der gesamte Produktionsprozess nicht nur automatisiert, sondern auch intelligent vernetzt wird. Diese Entwicklung hat enorme Auswirkungen auf die Produktionsgeschwindigkeit, die Personalisierung von Produkten und den intelligenten Einsatz von Ressourcen. Somit ist der Schritt von Produktion 3.0 zu 4.0 nicht nur eine inkrementelle Verbesserung, sondern vielmehr ein Paradigmenwechsel, der die gesamte Wirtschaft und die Art und Weise, wie wir produzieren, verändert.
Die Evolution der Produktion: Von 3.0 zu 4.0
Der Weg von Produktion 3.0 zu 4.0 markiert einen signifikanten Wandel in der Industrielandschaft. Die Haupttreiber dieser Evolution sind Fortschritte in der Technologie sowie wandelnde Erwartungen seitens der Kundschaft und des Marktes. Während in der Phase der Produktion 3.0 die Automatisierung zur Effizienzsteigerung im Vordergrund stand, zeichnet sich Produktion 4.0 durch eine intelligente Vernetzung aus, die eine neue Stufe der Produktionsintelligenz einläutet.
Einer der Schlüsselfaktoren dieser Veränderung ist die zunehmende Datenverfügbarkeit. Informationen werden in Echtzeit gesammelt und ausgewertet, um Prozesse zu optimieren und Anpassungen dynamisch vorzunehmen. Zudem ermöglicht die Integration von cyber-physischen Systemen (CPS) eine noch nie dagewesene Abstimmung zwischen physischen Komponenten und der digitalen Steuerungsebene. Dies erlaubt einen nahtlosen Informationsaustausch und eine adaptive Prozesskontrolle.
Die Evolution hin zu Produktion 4.0 bringt auch eine verstärkte Kundenorientierung mit sich. Individuelle Kundenwünsche können durch flexible Produktionsprozesse schneller und präziser umgesetzt werden. Das Konzept der Massenanpassung (Mass Customization) wird somit Realität und löst die traditionelle Massenproduktion mehr und mehr ab.
In dieser Übergangsphase werden menschliche Arbeit und automatisierte Systeme neu definiert. Die Mitarbeiterinnen und Mitarbeiter erlangen eine zentralere Rolle, indem sie durch Assistenzsysteme unterstützt werden und in hochkomplexen Entscheidungsprozessen als entscheidende Schnittstelle agieren.
Der Vergleich von Industrie 3.0 und Industrie 4.0
Kriterium | Produktion 3.0 (Industrie 3.0) | Produktion 4.0 (Industrie 4.0) |
---|---|---|
Technologie | Automatisierung durch Elektronik und IT | Internet der Dinge und Dienste, Cyber-physische Systeme |
Anpassungsfähigkeit | Begrenzt flexibel, hohe Losgrößen | Hochflexibel, individualisierte Massenproduktion |
Optimierung | Optimierung einzelner Maschinen | Gesamtsystemoptimierung, Ressourceneffizienz |
Daten | Isolierte Datennutzung | Integration und Vernetzung von Datenströmen |
Kommunikation | Limitierter Informationsaustausch | Nahtlose Kommunikation in Echtzeit |
Arbeitsweise | Funktions-/Arbeitsteilung | Kollaborative, vernetzte Arbeitsprozesse |
Entscheidungsfindung | Zentralisierte Entscheidungen | Dezentrale Entscheidungsfindung, Autonomie |
Wartung | Präventive Wartung | Zustandsorientierte und vorausschauende Wartung |
Produktivität | Massenproduktion, Effizienzsteigerungen durch Skaleneffekte | Optimierung durch Flexibilität und Individualisierung, Effizienz durch Integration und Intelligenz |
Rolle des Menschen | Bediener von Maschinen und Anlagen | Entscheider und Problemlöser mit IT-Unterstützung |
Kernmerkmale der Produktion 3.0
Produktion 3.0 kennzeichnete einen Wendepunkt in der industriellen Fertigung, an dem sich der Fokus auf die Automatisierungstechnik richtet. Kernmerkmale, die diese Produktionsphase ausmachen, sind unter anderen die Implementierung von programmierbaren Logiksteuerungen (PLC) und die Nutzung von Robotern in der Fertigung. Diese Komponenten ermöglichen eine effizienzorientierte und schnellere Produktion und verringern die Abhängigkeit von menschlicher Arbeitskraft an repetitiven und physisch anstrengenden Stellen.
Ein weiteres Kennzeichen der Produktion 3.0 ist die Einführung von Fertigungszellen, in denen Roboter und Maschinen für spezifische Aufgaben konzipiert und angeordnet sind. Dies fördert die Modularität und Flexibilität in der Produktion. Zudem erhöht es die Skalierbarkeit, da durch standardisierte Schnittstellen unterschiedliche Module leicht ausgetauscht oder erweitert werden können.
Die Digitalisierung nimmt in Produktion 3.0 ihren Anfang, wobei Computer Aided Design (CAD) und Computer Aided Manufacturing (CAM) essenziell für die Entwicklung und Produktion von Erzeugnissen sind. Diese Softwarelösungen unterstützen die präzise Konstruktion und Fertigung von Produkten und sind ein bedeutsamer Schritt hin zur Verbindung von digitaler und physischer Welt.
Zusammenfassend kann festgehalten werden, dass die Kernmerkmale der Produktion 3.0 vor allem auf den technologischen Fortschritt in der Automatisierungstechnologie zurückzuführen sind, welche die Grundsteine für die spätere Entwicklung zur Produktion 4.0 legten.
Innovationen und Technologien in der Produktion 4.0
Die Produktion 4.0 zeichnet sich durch den Einsatz wegweisender Innovationen und Technologien aus, die eine intelligente und vernetzte Fertigungsumgebung schaffen. Ein zentrales Element ist das Internet der Dinge (IoT), welches Maschinen, Produkte und Menschen in Echtzeit miteinander verbindet. Dies ermöglicht eine kontinuierliche Datenerfassung und -analyse zur Prozessoptimierung und vorbeugenden Instandhaltung.
Des Weiteren spielt die künstliche Intelligenz (KI) eine tragende Rolle. Sie befähigt Maschinen dazu, eigenständig Muster zu erkennen, Entscheidungen zu treffen und somit Prozesse selbst zu steuern. Durch maschinelles Lernen werden Anlagen im Laufe der Zeit zudem immer effizienter und genauer.
Ein weiteres Kernmerkmal sind cyber-physische Systeme (CPS), die über Sensoren und Aktoren direkt mit der digitalen Welt verbunden sind und einen reibungslosen und flexiblen Produktionsablauf sicherstellen. Diese Systeme bilden das Rückgrat der smarten Fabriken, in denen physische und digitale Prozesse verschmelzen.
Digitale Zwillinge, also virtuelle Abbilder von physischen Objekten oder Prozessen, bilden ebenfalls eine Basisinnovation der Produktion 4.0. Sie erlauben es, Produkte oder Produktionsabläufe in einer virtuellen Umgebung zu simulieren, zu analysieren und zu optimieren, bevor sie in der realen Welt implementiert werden.
Darüber hinaus ermöglichen Additive Fertigungsverfahren, wie der 3D-Druck, eine flexible und kosteneffiziente Produktion von individuell gestalteten Produkten und Komponenten. Diese Technologien sind besonders relevant für die kundenindividuelle Massenfertigung (Mass Customization) und die schnelle Herstellung von Prototypen.
Cloud-Computing und Big Data-Analysen gehören ebenfalls zu den Innovationen der Produktion 4.0, die eine übergeordnete Datenverarbeitung und -auswertung in großer Menge und Geschwindigkeit ermöglichen. Diese Aspekte bilden das Fundament für fundierte Entscheidungsprozesse und eine zukunftsorientierte, agile Produktionsumgebung.
Vergleich: Effizienz und Flexibilität in Produktion 3.0 und 4.0
Die Gegenüberstellung von Produktion 3.0 und 4.0 hinsichtlich ihrer Effizienz und Flexibilität offenbart den progressiven Charakter der industriellen Entwicklung. In Produktion 3.0 führte der Einsatz von Automatisierungstechnik bereits zu beträchtlichen Effizienzgewinnen. Fabriken konnten schneller und kostengünstiger produzieren, indem sie repetitive und einfache Aufgaben automatisierten. Doch die Flexibilität war oft eingeschränkt, da Umstellungen auf neue Produkttypen zeitaufwendig und kostspielig sein konnten.
Produktion 4.0 hebt die Effizienz und Flexibilität auf ein neues Niveau. Durch den Einsatz vernetzter Systeme können Produktionsprozesse selbstadaptiv und somit effizienter gestaltet werden. Änderungen im Produktionsablauf oder individuelle Kundenwünsche können nun schneller umgesetzt werden, was eine hohe Flexibilität auch bei komplexen Produktionsprozessen ermöglicht.
Die Echtzeitdatenanalyse spielt eine entscheidende Rolle bei der Steigerung der Effizienz in Produktion 4.0. Sie ermöglicht es, Produktionsabläufe fortlaufend zu optimieren und Ressourcenverbräuche zu minimieren. Dies steht im Kontrast zu Produktion 3.0, in welcher die Datenverarbeitung oft nicht in Echtzeit erfolgte und somit weniger reaktionsfähig gegenüber unmittelbaren Herausforderungen war.
Die Schaffung von modularen und rekonfigurierbaren Systemen in Produktion 4.0 unterstützt die Idee einer flexiblen Fertigung, die ohne großen Aufwand umgestaltet werden kann. Im Vergleich hierzu konnten solche Systeme in Produktion 3.0 nur mit einem merklichen Mehraufwand an Zeit und Investitionen verändert werden.
Zusammenfassend zeigt der Vergleich die Überlegenheit von Produktion 4.0 in puncto Effizienz und Flexibilität auf, die durch fortschrittliche Technologien und Konzepte wie IoT, KI und cyber-physische Systeme ermöglicht werden.
Auswirkungen der Produktion 4.0 auf die Arbeitswelt
Die Einführung der Produktion 4.0 führt zu grundlegenden Veränderungen in der Arbeitswelt. Der Wandel beeinflusst nicht nur Produktionsprozesse, sondern auch die Rolle der Menschen, die in diesem Umfeld tätig sind. Einer der signifikantesten Effekte ist die Verlagerung von manuellen Tätigkeiten zu überwachenden und kontrollierenden Funktionen. Arbeitnehmer müssen daher in der Lage sein, komplexere Systeme zu steuern und die von Maschinen erzeugten Daten zu interpretieren.
Die Kompetenzanforderungen verschieben sich also in Richtung technologisches Wissen und IT-Kenntnisse. Arbeitnehmer müssen lernen, mit neuen Technologien wie KI-Systemen und Analyse-Tools umzugehen. Durch die höhere Komplexität in der Produktion wird zudem die berufliche Weiterbildung immer wichtiger, um Schritt mit den technologischen Entwicklungen halten zu können.
Die Vernetzung verschiedener Bereiche bringt auch eine stärkere Kollaboration zwischen verschiedenen Abteilungen mit sich. Mitarbeiter aus der Produktion, IT und der Entwicklungsabteilung müssen enger zusammenarbeiten, um die umfassenden Vorteile von Produktion 4.0 nutzen zu können. Dies erfordert effektive Kommunikationsfähigkeiten und ein Verständnis für interdisziplinäre Zusammenhänge.
Ein weiterer Aspekt ist die Flexibilisierung der Arbeitsplätze. Produktion 4.0 kann Standortunabhängigkeit und flexible Arbeitszeiten begünstigen, wenn beispielsweise Steuerungs- oder Wartungsaufgaben aus der Ferne durchgeführt werden können.
Abschließend lässt sich feststellen, dass die Auswirkungen der Produktion 4.0 auf die Arbeitswelt weitreichend sind. Sie verlangen eine Anpassungsfähigkeit der Arbeitnehmer an neue Technologien, eine Neigung zur kontinuierlichen Weiterentwicklung der eigenen Fähigkeiten und die Bereitschaft zur interdisziplinären Zusammenarbeit.
Nachhaltigkeit und Umweltschutz: Produktion 3.0 gegenüber 4.0
Die Themen Nachhaltigkeit und Umweltschutz erhalten in der Produktion 4.0 einen neuen Stellenwert. Während in der Ära der Produktion 3.0 die Automatisierung und Effizienzsteigerung häufig ohne umfassende Berücksichtigung ökologischer Aspekte stattfand, steht in der intelligenten Produktion das Ziel einer ressourcenschonenden Fertigung im Vordergrund.
In Produktion 4.0 sorgen intelligente Analysesysteme und prozessintegrierte Sensoren dafür, dass Ressourcenverbrauch und Abfälle minimiert werden. Dies ist möglich, da Maschinen und Anlagen präzise auf den Bedarf abgestimmt arbeiten und Energie sowie Materialien effizienter genutzt werden. Dementsprechend fallen weniger überschüssige Rohstoffe und Energieverschwendung an als zuvor.
Mit Hilfe von geschlossenen Kreislaufsystemen und einer stärkeren Fokussierung auf die Kreislaufwirtschaft können Materialien recycelt und wiederverwendet werden. Dies reduziert nicht nur die Umweltbelastung, sondern auch die Abhängigkeit von neuen Rohstoffen. Die Herangehensweise in Produktion 4.0 ist daher ganzheitlich und berücksichtigt den gesamten Lebenszyklus eines Produktes.
Die Optimierung von Produktionsprozessen trägt zusätzlich zum Umweltschutz bei, indem Transportwege verkürzt und Lagerbestände reduziert werden. Die Lieferkette wird schlanker und effizienter, was ebenfalls dazu beiträgt, den Kohlenstoff-Fußabdruck der Produktion zu verringern.
Zusammenfassend ist erkennbar, dass Produktion 4.0 im Vergleich zur Produktion 3.0 bedeutende Vorteile für Nachhaltigkeit und Umweltschutz mit sich bringt. Sie nutzt fortgeschrittene Technologien und Systeme, um ökologische Ziele in Einklang mit wirtschaftlicher Effizienz zu bringen.
Herausforderungen bei der Umstellung von Produktion 3.0 auf 4.0
Die Umstellung von Produktion 3.0 auf 4.0 bringt diverse Herausforderungen mit sich, die Unternehmen bewältigen müssen. Eine zentrale Herausforderung ist die notwendige Investition in neue Technologien und Infrastrukturen. Die Anschaffung von intelligenten Maschinen, Sensoren und die Implementierung von IT-Systemen, welche die Basis für eine vernetzte Produktion darstellen, erfordern eine finanzielle Grundlage, die nicht jedes Unternehmen sofort bereitstellen kann.
Des Weiteren stellt die Sicherheit von Daten eine wesentliche Herausforderung dar. Mit dem zunehmenden Grad der Vernetzung steigt auch das Risiko von Cyberangriffen und Datenlecks. Unternehmen müssen daher in robuste Sicherheitssysteme investieren und ihre Mitarbeiter im Umgang mit sensiblen Daten schulen.
Das erforderliche Know-how für den Betrieb und die Wartung hochtechnologischer Systeme ist nicht in jedem Unternehmen vorhanden. Fachkräfte mit entsprechenden Kompetenzen sind gefragt, was zu Engpässen auf dem Arbeitsmarkt führen kann. Aus diesem Grund sind Fortbildung und Umschulung bestehender Mitarbeiter entscheidend, um die Kompetenzlücke zu schließen.
Die Integration von Altsystemen in die neue Produktionsumgebung ist ein weiterer wichtiger Punkt. Viele Maschinen und Anlagen müssen aufgerüstet oder durch kompatible Systeme ersetzt werden, um eine nahtlose Kommunikation innerhalb der vernetzten Produktion zu ermöglichen.
Zudem ist die unternehmensweite Akzeptanz für den Wandel von Produktion 3.0 zu 4.0 entscheidend. Widerstand gegen Neuerungen und ein Festhalten an etablierten Prozessen können die Transformation behindern. Deshalb ist es wichtig, die Belegschaft frühzeitig einzubeziehen und den Nutzen der Veränderungen transparent zu machen.
Fallbeispiele: Unternehmen im Wandel zur Produktion 4.0
Verschiedene Unternehmen weltweit fungieren als Pioniere im Übergang zur Produktion 4.0. Ein exemplarisches Fallbeispiel ist ein deutscher Automobilhersteller, der in seinen Werken Smart Factories etablierte. Durch eine vollständige Vernetzung des Produktionsprozesses und den Einsatz autonomer Fertigungsroboter konnte eine Flexibilisierung der Fertigungslinien erreicht werden. Individuelle Kundenwünsche lassen sich auf diese Weise effizient in die Produktionsabfolge integrieren.
Ein weiteres Beispiel ist ein Hersteller von Industrieausrüstung, der den Einsatz von digitalen Zwillingen realisierte. Dabei werden reale Anlagen in einem virtuellen Modell nachgebaut, um Simulationen und Optimierungen durchzuführen. Dieses Verfahren ermöglicht eine deutliche Reduktion von Entwicklungszeiten und verbesserter Produktqualität.
In der Prozessindustrie zeigt ein Chemiekonzern, wie durch die Integration von Sensortechnologie und Big-Data-Analysen eine ressourceneffiziente Produktion gefördert wird. Die vollständige Überwachung und Analyse der Produktionsabläufe führt zu einer Senkung des Energieverbrauchs und zur Reduktion von Abfallprodukten.
Durch die Einführung sogenannter Cobots, also kollaborierender Roboter, gelang es einem Logistikunternehmen, die Zusammenarbeit zwischen Menschen und Maschinen zu optimieren und dadurch die Lager- und Versandprozesse signifikant zu beschleunigen.
Diese Fallbeispiele zeigen, dass der Übergang zur Produktion 4.0 in verschiedenen Branchen und Unternehmensgrößen zum Tragen kommt und es ermöglicht, Prozesse zu optimieren, Produktivität zu steigern und auf individuelle Kundenbedürfnisse präziser einzugehen.
Zukunftsperspektiven: Wie Produktion 4.0 die Industrie transformiert
Die Zukunftsperspektiven in Bezug auf Produktion 4.0 versprechen eine weitreichende Transformation der Industrie. Die umfassende Digitalisierung und Vernetzung führen zu einer deutlich gesteigerten Agilität von Unternehmen. Sie werden in die Lage versetzt, schneller auf Marktveränderungen und individuelle Anforderungen zu reagieren, Produktentwicklungszeiten zu reduzieren und neue Geschäftsmodelle zu entwickeln.
Ein zentraler Aspekt künftiger Produktionsumgebungen wird die weitere Personalisierung von Erzeugnissen sein. Die Fähigkeit, Produkte in Losgröße 1 kosteneffizient herzustellen, könnte die Massenfertigung standardisierter Produkte ablösen und neue Möglichkeiten für Nischenmärkte und -produkte eröffnen.
Das Thema Nachhaltigkeit wird durch Produktion 4.0 zusätzlich gefördert. Innovative Technologien ermöglichen es, Ressourcen optimal zu nutzen und Abfall sowie Emissionen zu reduzieren. Hierdurch leistet die Industrie einen wesentlichen Beitrag zum Umweltschutz und zur Schonung natürlicher Ressourcen.
Auch wird die Bedeutung von Serviceleistungen zunehmen, da Produktion 4.0 eine engere Kundenbindung und eine Verlängerung des Produktlebenszyklus durch Wartung und Upgrades ermöglicht. Dadurch ergeben sich neue Potenziale im Kundenservice und After-Sales-Bereich.
In der Vorschau auf die nächsten Jahre zeigt sich, dass Unternehmen, die die Prinzipien der Produktion 4.0 annehmen, einen signifikanten Wettbewerbsvorteil erlangen können. Die Industrie wird smarter, kundenorientierter und nachhaltiger und schafft somit die Grundlage für eine erfolgreiche Zukunft.
Fazit: Die Bedeutung des Übergangs von Produktion 3.0 zu 4.0
Der Übergang von Produktion 3.0 zu 4.0 stellt eine signifikante Entwicklung in der industriellen Fertigung dar. Dieser Schritt symbolisiert nicht nur den technologischen Fortschritt, sondern auch eine Neuausrichtung der Produktionsprozesse hin zu mehr Effizienz, Anpassungsfähigkeit und Nachhaltigkeit. Unternehmen, die diesen Wandel vollziehen, können von einer verbesserten Wettbewerbsfähigkeit und der Fähigkeit profitieren, schnell auf ein sich ständig veränderndes Marktumfeld zu reagieren.
Wichtig ist die Erkenntnis, dass der Wechsel zu Produktion 4.0 eine umfassende strategische Planung erfordert. Die Investition in fortschrittliche Technologien und die Weiterbildung der Belegschaft sind entscheidend für den Erfolg dieser Transformation. Zugleich müssen potenzielle Risiken wie Datenschutz und IT-Sicherheit sorgfältig gemanagt werden.
Der Übergang zu einer intelligenten Fabrik ist somit weit mehr als ein technologischer Schritt – er ist eine Chance für Unternehmen, ihre Produktionsweise zu revolutionieren, die Beziehung zu ihren Kunden neu zu definieren und aktiv zur Schonung der Umwelt beizutragen. Somit markiert Produktion 4.0 den Beginn eines neuen Zeitalters industrieller Fertigung, das mit aufregenden Möglichkeiten für Innovation und Wachstum einhergeht.
Produkte zum Artikel
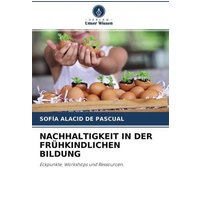
43.90 EUR* * inklusive % MwSt. / Preis kann abweichen, es gilt der Preis auf dem Onlineshop des Anbieters.
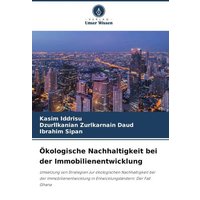
71.90 EUR* * inklusive % MwSt. / Preis kann abweichen, es gilt der Preis auf dem Onlineshop des Anbieters.
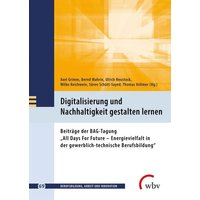
54.90 EUR* * inklusive % MwSt. / Preis kann abweichen, es gilt der Preis auf dem Onlineshop des Anbieters.
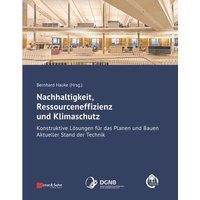
29.90 EUR* * inklusive % MwSt. / Preis kann abweichen, es gilt der Preis auf dem Onlineshop des Anbieters.
Häufig gestellte Fragen: Der Wandel von traditioneller zu intelligenter Fertigung
Was ist der grundlegende Unterschied zwischen Produktion 3.0 und Produktion 4.0?
Der grundlegende Unterschied liegt in der Vernetzung und Intelligenz der Produktionssysteme. Produktion 3.0 konzentriert sich auf Automatisierung mittels Robotik und elektronischer Steuerungssysteme. Produktion 4.0 hingegen bezieht sich auf eine smart vernetzte Produktion, die eine breite Palette von Technologien wie das Internet der Dinge (IoT), Big Data, KI und cyber-physische Systeme nutzt, um Effizienz, Anpassungsfähigkeit und Echtzeitoptimierung zu verbessern.
Inwiefern beeinflusst Produktion 4.0 die Entscheidungsfindung in Unternehmen?
Produktion 4.0 ermöglicht durch die Vernetzung von Maschinen und die Nutzung von Datenanalysen eine dezentralere Entscheidungsfindung. Systeme können autonom Entscheidungen treffen und flexibel auf Veränderungen reagieren, was zu einer agileren und effizienteren Produktionsweise führt und menschliche Mitarbeiter von repetitiven Entscheidungen entlastet.
Wie trägt Produktion 4.0 zur Personalisierung von Produkten bei?
Produktion 4.0 vereinfacht die Massenanpassung (Mass Customization) durch Anlagen, die schnell rekonfiguriert werden können, um individuelle Kundenwünsche zu erfüllen. Die enge Integration von Kundeninteraktionssystemen ermöglicht es, spezifische Produktspezifikationen direkt in den Fertigungsprozess zu integrieren, wodurch Produkte personalisiert hergestellt werden können ohne die Effizienz der Massenproduktion einzubüßen.
Welche Rolle spielen Daten in der Produktion 4.0?
Daten sind das Herzstück der Produktion 4.0 und ermöglichen es, alle Aspekte der Produktion zu überwachen und zu optimieren. Sie werden in Echtzeit gesammelt, analysiert und genutzt, um Prozesse effizienter zu gestalten, die Wartung zu verbessern und die Produktqualität zu sichern. Durch die Sammlung und Vernetzung von Daten können Prozesse kontinuierlich verbessert und angepasst werden.
Welche Herausforderungen müssen Unternehmen bei der Umstellung auf Produktion 4.0 meistern?
Die Umstellung auf Produktion 4.0 erfordert signifikante Investitionen in neue Technologien, die Schulung von Mitarbeitern, die Gewährleistung der Cybersicherheit und die Integration bestehender Systeme. Unternehmen müssen eine Kultur der Veränderungsbereitschaft schaffen, die sowohl technologische als auch organisatorische Transformation umfasst, und sie müssen mit Herausforderungen wie dem Datenschutz und der Notwendigkeit einer kontinuierlichen Innovation umgehen.